Plastic extrusion for efficient, scalable manufacturing solutions
Plastic extrusion for efficient, scalable manufacturing solutions
Blog Article
A Comprehensive Overview to the Process and Advantages of Plastic Extrusion
In the huge realm of production, plastic extrusion arises as a extremely efficient and crucial procedure. Translating raw plastic into constant accounts, it provides to a variety of sectors with its exceptional convenience.
Recognizing the Fundamentals of Plastic Extrusion
While it may appear facility in the beginning glance, the process of plastic extrusion is basically easy - plastic extrusion. It is a high-volume manufacturing technique in which raw plastic is melted and shaped right into a continuous account. The procedure starts with the feeding of plastic product, in the kind of granules, powders, or pellets, right into a warmed barrel. The plastic is after that thawed using a mix of warm and shear, applied by a revolving screw. Once the molten plastic reaches the end of the barrel, it is required with a tiny opening called a die, forming it into a desired type. The designed plastic is after that cooled, strengthened, and cut right into desired lengths, completing the procedure.
The Technical Refine of Plastic Extrusion Explained
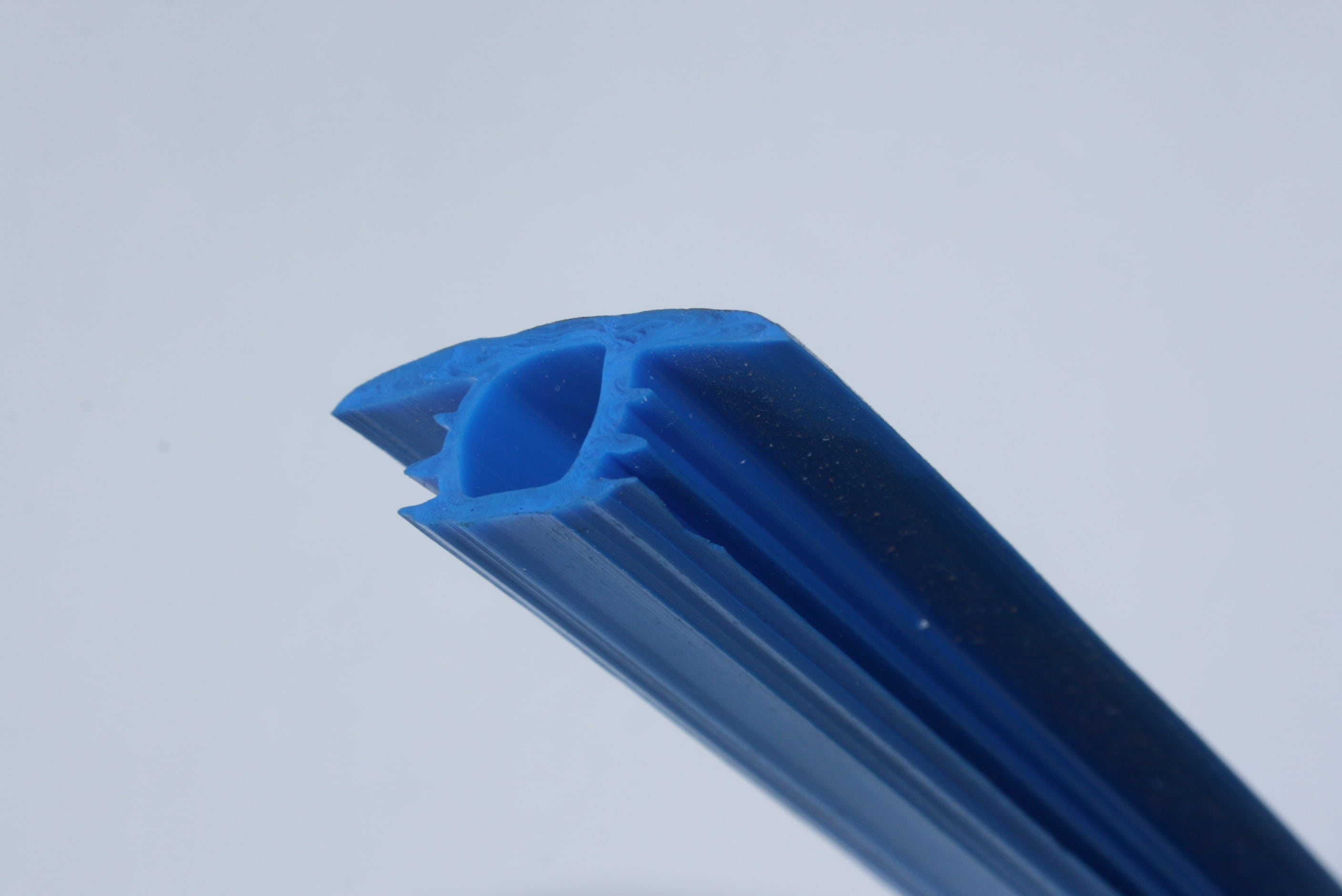
Types of Plastic Suitable for Extrusion
The selection of the right sort of plastic is a crucial element of the extrusion process. Various plastics provide distinct residential properties, making them more matched to specific applications. Polyethylene, for instance, is commonly made use of due to its inexpensive and simple formability. It supplies excellent resistance to chemicals and moisture, making it optimal for products like tubing and containers. Polypropylene is an additional prominent option due to its high melting point and resistance to exhaustion. For even more durable applications, polystyrene and PVC (polyvinyl chloride) are frequently chosen for their strength and durability. These are typical alternatives, the selection inevitably depends on the specific needs of the product being produced. Recognizing these plastic types can dramatically improve the extrusion procedure.
Contrasting Plastic Extrusion to Various Other Plastic Forming Techniques
Understanding the types of plastic ideal for extrusion paves the way for a broader conversation on just how plastic extrusion stacks up versus other plastic creating approaches. Plastic extrusion is exceptional when it comes to creating constant profiles, such as pipelines, seals, and gaskets. my site It likewise allows for a constant cross-section along the length of the product.
Secret Benefits of Plastic Extrusion in Manufacturing
In the world of production, plastic extrusion offers several considerable benefits. One remarkable benefit is the cost-effectiveness of the procedure, which makes it a financially appealing production approach. Additionally, this method provides superior product adaptability and boosted manufacturing rate, thereby boosting total production effectiveness.
Cost-efficient Production Approach
Plastic extrusion leaps to the center as a cost-efficient manufacturing technique in production. This procedure stands apart for its capability to generate high quantities of product swiftly and efficiently, supplying manufacturers with substantial cost savings. The primary price advantage is the ability to use less costly basic materials. Extrusion utilizes thermoplastic materials, which are much less pricey compared to metals or porcelains. Further, the extrusion procedure itself is relatively easy, reducing labor costs. In addition, plastic extrusion requires less energy than conventional manufacturing methods, adding to lower functional prices. The process also reduces waste, as any kind of excess or defective products can be recycled and reused, offering an additional layer of cost-effectiveness. Generally, the financial benefits make plastic extrusion a highly eye-catching alternative in the production market.

Superior Product Flexibility
Past the cost-effectiveness of plastic extrusion, an additional substantial advantage in manufacturing lies in its premium product flexibility. This process permits for the production of a vast range of items with varying dimensions, styles, and forms, from straightforward plastic sheets to complex accounts. The flexibility is credited to the extrusion die, which can be personalized to yield the desired product design. This makes plastic extrusion a suitable solution for industries that call for customized plastic elements, such as vehicle, building, and packaging. The ability to generate diverse items is not only valuable in meeting specific market demands yet look what i found additionally in allowing manufacturers to check out brand-new product with marginal capital financial investment. In essence, plastic extrusion's item versatility promotes technology while enhancing operational performance.
Enhanced Production Speed
A substantial benefit of plastic extrusion lies in its enhanced production rate. Few various other manufacturing procedures can match the speed of plastic extrusion. Additionally, the capability to maintain constant high-speed production look at this now without giving up item quality sets plastic extrusion apart from various other techniques.
Real-world Applications and Impacts of Plastic Extrusion
In the realm of manufacturing, the method of plastic extrusion holds extensive value. The economic benefit of plastic extrusion, largely its economical and high-volume outcome, has actually transformed production. The sector is persistently making every effort for developments in biodegradable and recyclable materials, suggesting a future where the advantages of plastic extrusion can be kept without jeopardizing ecological sustainability.
Final thought
To conclude, plastic extrusion is a very reliable and effective method of changing resources into diverse products. It provides various benefits over various other plastic forming methods, consisting of cost-effectiveness, high outcome, marginal waste, and design flexibility. Its impact is profoundly really felt in various industries such as construction, auto, and customer goods, making it an essential procedure in today's production landscape.
Diving deeper right into the technical process of plastic extrusion, it starts with the option of the ideal plastic material. Once cooled, the plastic is cut into the called for sizes or wound onto reels if the item is a plastic movie or sheet - plastic extrusion. Comparing Plastic Extrusion to Other Plastic Forming Methods
Understanding the types of plastic ideal for extrusion leads the means for a broader discussion on just how plastic extrusion piles up versus other plastic developing techniques. Couple of other production processes can match the speed of plastic extrusion.
Report this page